Whenever you are trying to produce any product part in a bulk, injection molding is the first process that comes to your mind. Known as a popular manufacturing process, injection molding has proven to be quite valuable for the consumer product development firm. Here, plastic remains the most common component for multiple consumer items. Injection molding is one best way to create those plastic parts in bulk, and with ease. While working on the injection molding process, there are three major parts to it. So, let’s delve into those details right now.
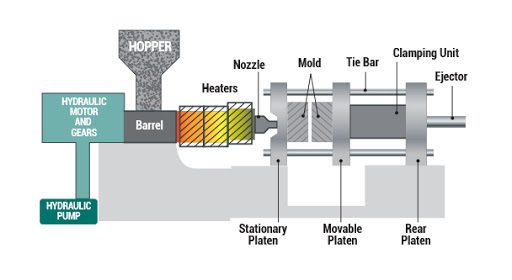
The first step – Product design:
One major facet of the production process has to be the design of the plastic item. If you want to avoid some expensive mistakes later, then you better focus on the design at its initial stage. You better determine the best idea first of all, before proceeding further with inserts in injection molding and creating the perfect result in the end.
- There are various objectives to be kept in mind while designing. Some of those are assembly, manufacturing ability, aesthetic, and function.
- The proper design will be that one, which can accomplish the possible requirements well to their satisfactory level. But, be prepared to use maximum creativity power to reach that goal.
- You can accomplish product design with CAD or computer-aided design software. SolidWorks is one such example to follow.
- Not just using CAD software, but you need to be proficient in its work. It helps you to work on quick iterations and ending up with an accurate prototype.
- You can avoid costly mistakes in the product designing stage by planning for uniform wall thickness when you can. Then you have to transit from one thickness to another with small steps when you can’t avoid the changes anymore. You should not build in stress inside the design.
Skilled design engineers are appointed to design and improve various solutions for matching the complexities of any specified project. The design team will work hard to combine their experiences to create promising solutions to intricate problems. They have been working in this sector for long and can help people get thoughtful results in the end.
Second step – Mold design:
After testing out the design and keeping it aside for further production, it is time to design the mold or die for injection molding. You can get experts from mold co ltd to help you in this regard. There are some common metals used for manufacturing molds. The first and most important one is hardened steel, which is the most expensive option. It makes the mold long-lasting. Then you have pre-hardened steel, which may not last as much as the previous example and is less expensive to work with. Then you have aluminum, which is used for prototype tooling. The last example is that of a beryllium-copper alloy. It is used in those molding areas in need of faster heat removal, or where the sheer heat remains concentrated.
You have to concentrate on the mold design properly in order to avoid expensive mistakes in the final injection molding process. Poor mold design is the last thing you want to avoid a costly mistake. Not properly designing the proper draft can lead to some serious mistakes. It mainly refers to an angle in which the finished item will be ejected from the mold.
Even improper placement of sizes of gates can be another mold mistake to work in the first place. Here, gates are mainly the opening in a mold through which you get to inject the thermoplastic material or thermostat. Each one will leave a scar, which results in functional or aesthetic issues if not placed properly.
The cycle parts and the materials of each one will help drive decision making on which materials you need to be working on.
Third stage – Manufacturing procedure:
After a product has been designed, die-cast, and approved properly, it is time to focus on the main manufacturing process. The thermostat remains in its granular form when fed through a hopper into a heating barrel. The plastic then gets heated to a designated temperature and driven through the gate into the mold. After filling the mold, the pressure is applied to give the predetermined shape. When the pressure is completely covered, the mold is opened up, and the part gets ejected.